Success Stories & Case Studies
Our Work
Leading Tea Manufacturer
We successfully implemented ERPNext software for one of India's leading tea manufacturers, with a presence in 10 states. With a vast network of 800+ distributors, 35+ super stockists, a 500+ strong sales team, and 70+ ERP users, the company required a robust and scalable solution. Our tailored ERPNext implementation streamlined their operations, enhanced inventory traceability, optimized production planning, and integrated procurement and distribution processes. This transformation has empowered them to operate more efficiently, make data-driven decisions, and scale their business seamlessly.
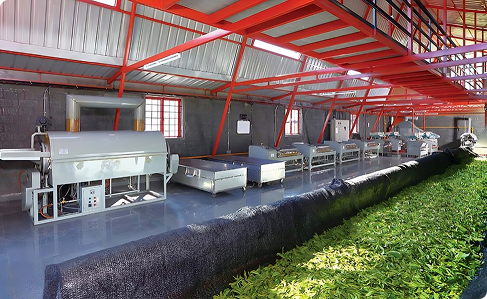
Challenges
- Limited Functionality with Existing Navision and Homegrown ERP
- Lack of Control Over Inventory and Manufacturing Processes
- Challenges with FIFO Maintenance and Inventory Management
- Absence of Price Lists and Scheme Management in System
- Lack of Integration for a 360-Degree Business View
- No Single Source of Truth for Data and Operations
- Difficulty in Accessing Data and Generating Reports
Work Done
- Successful Go-Live with All Modules in One Go
- Territory-Level Branch Accounting in ERPNext System
- Customised ERP Solution for Blending Processes
- Scheme Management at Sales Order and Delivery Levels
- MRP with Inventory Traceability and Batch Printing Integration
- Integrated ERP with Procurement, WMS, and DMS Systems
- Multi-UoM Stock Management for Bags, Kg, and Packets
Benefits
- Streamlined Operations with Unified Modules
- Accurate Financial Tracking by Territory
- Optimized Production Through Custom Blending
- Efficient Sales and Scheme Management
- Enhanced Inventory Traceability and Compliance
- Seamless Integration Across Key Systems
- Flexible and Precise Inventory Management
Leading Vegetable Seed Company
We successfully implemented ERPNext software for a leading vegetable seed company in India, with over 30 years of experience in seed production, marketing, and distribution. With a presence in 10 countries and across all states in India, and 13 sales distribution centers, the company needed a robust solution for managing its vast operations. Our ERPNext implementation streamlined their processes, from sales and inventory management to production and distribution. The system has empowered over 120 ERP users, enabling better decision-making, improved operational efficiency, and seamless integration across their subsidiaries in Thailand and Sri Lanka.
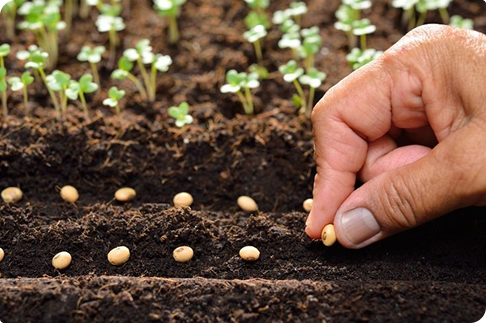
Challenges
- Challenges in Linking Procurement, Quality, and Processing
- Difficulty Managing Growers as Both Suppliers and Customers
- Issues with Maintaining Secrecy and Parent-Child Relationships
- Quality Management Process Was Inefficient
- Absence of Stage-Wise, Lot-Wise Item Stock Tracking
- Manual Lot Number Maintenance for Future Reference
- Lack of Structured Master Data and Defined SOP
Work Done
- Seamless Go-Live Across 13 Depots and 5 Centers
- Integrated Supply Chain and Processing Operations
- Automated Quality Inspections for Faster Payments
- Improved Quality Control at Purchase and Stock Levels
- Efficient Batch Management with Automated Lot Creation
- Secure Data Access by Territory and Branch
- Timely Grower Payments with Automated Workflow.
Benefits
- Streamlined Operations Across Depots and Centers
- Faster Grower Payments Through Automation
- Consistent Product Quality Control
- Enhanced Inventory Management and Traceability
- Improved Data Security with Restricted Access
- Optimized Supply Chain and Production Efficiency
- Accurate, Real-Time Data for Better Decision-Making
Swiss-Indian Agritech
We successfully implemented ERPNext software for a Swiss-Indian agritech group focused on consolidating the food chain onto a single platform. The group comprises 20 companies, including 4 operational, 9 trading, and 7 holding companies across 7 countries, with 5 distinct lines of business. Our ERPNext solution streamlined their diverse operations, integrating key processes across multiple business units. This transformation has empowered the group to gain better visibility, enhance operational efficiency, and make data-driven decisions, enabling them to manage their complex global business with ease.
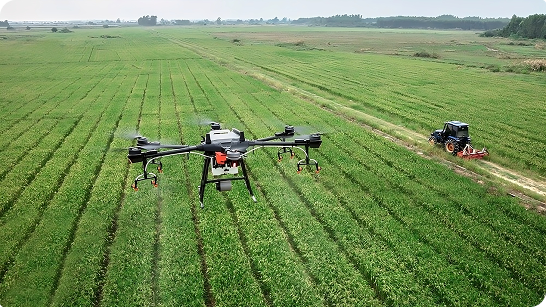
Challenges
- Complex System Architecture with Extensive Platform Integration
- Lack of Single Source of Truth Across 20 Companies
- Limited Visibility into Product Origin and Movement
- Challenges with E-Commerce Payment Structures
- Gaps in Statutory Compliance for Goods Movement
- Inconsistent Accounting Transactions Across Platforms
- Inadequate Tracking for Effective Performance Review
Work Done
- Core Modules Implementation Across Distribution and Storage Locations
- QR Code-Based Batch Inventory Tracking for Enhanced Visibility
- Clear Payment Structure for Distinct Trading and Accounting
- ERP Integration with Farmlink eCommerce for Sales Order Capture
- Customisation for Landed Cost Management and Workflow Optimisation
- Enhanced Inventory Management with Real-Time Product Movement
- Streamlined Trading and Orchestration Accounting Processes
Benefits
- Optimized Operations Across Distribution and Storage
- Improved Product Traceability with Batch Tracking
- Efficient Payment and Accounting Structures
- Seamless Sales Order Capture from eCommerce Platform
- Accurate Landed Cost Management for Better Profitability
- Enhanced Inventory Visibility and Control
- Streamlined Orchestration Workflows for Faster Execution
Leading Precision Component Manufacturer
We successfully implemented ERPNext software for a leading precision component manufacturer serving the Oil and Gas, Food & Dairy, and Defence & Aerospace industries. Known for providing high-quality machining solutions that meet stringent industry standards, the company sought a robust platform to enhance operational efficiency. Our ERPNext solution streamlined their manufacturing processes, improved inventory management, and provided better control over production workflows. This integration has enabled them to meet the demands of their global clients more effectively, fostering innovation, excellence, and seamless business operations across all their divisions.
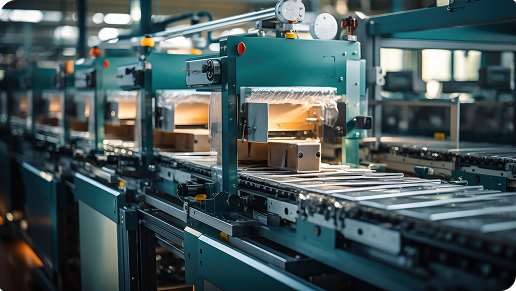
Challenges
- Data Consolidation Challenges with Separate Excel Sheets
- No Inquiry Tracking System for Production Reconciliation
- Manual Item Creation Leads to Errors and Duplications
- Inefficient Management of Party Addresses and Contacts
- Lack of Documentation for Effective Customer Follow-Up
- Manual Preventive Maintenance Planning Causes Inefficiencies
- Complex and Error-Prone Quality Inspection Reporting
- Mismatched Purchase Receipts and Orders Lead to Errors
- Manual Material Request System Impacts Tracking and Records
Work Done
- Centralized System for Improved Reporting and Data Integration
- Real-Time Inquiry Management Linked to Production
- Automated Item Creation to Reduce Errors and Duplication
- Efficient CRM for Managing Party Addresses and Contacts
- Task Management for Better Customer Meeting Follow-Ups
- Automated Preventive Maintenance for Enhanced Asset Management
- Centralized Quality Inspection Reports Integrated with Production
- Automated Purchase Receipt Matching for Accurate Financial Records
- Electronic Material Request System for Improved Tracking
Benefits
- Improved Reporting Accuracy and Reliability
- Real-Time Inquiry Tracking for Faster Response
- Reduced Errors and Duplication Through Automated Item Creation
- Streamlined Contact and Address Management in CRM
- Better Follow-Up with Task Management for Customer Meetings
- Enhanced Asset Management with Automated Maintenance Scheduling
- Centralized Quality Control for Consistent Production Standards
- Accurate Financial Records with Automated Purchase Matching
- Improved Material Tracking and Efficient Inventory Planning
Government Contracting and Trading Firm
We successfully implemented ERPNext software for a government contracting firm specializing in Mid-Day Meal (MDM) programs for schools, ICDS initiatives, Tribal Development, and Workers Welfare projects. The ERPNext solution streamlined their complex operations, including the distribution of meals, essential kits, and invoicing processes across multiple government departments. With project-wise accounting, real-time reporting, and improved compliance management, the company has achieved enhanced efficiency, better transparency, and seamless coordination, enabling them to effectively meet their contractual obligations and support welfare initiatives at scale.
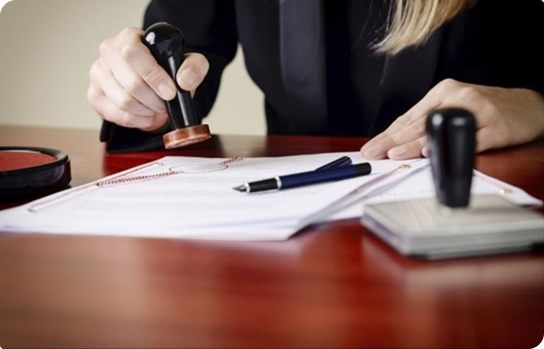
Challenges
- Limited Visibility into Project Progress and Profitability
- No Control Over Inventory and Manufacturing Processes
- Distribution Planning in Excel Led to Mistakes
- Lack of Control Over Deliveries and Manual Reconciliation
- Difficult Access to Consolidated Data and Reports
- Relying on Tally and Projectwise Applications for Management
- Inefficient Use of Excel for Critical Operations
Work Done
- Go-Live with Project-Wise Accounting in ERPNext
- Streamlined Grain and Pulse Distribution for Schools
- Efficient Meal and Kit Distribution for Construction Sites
- Accurate Multi-Level Invoicing for Government Departments
- Detailed Project-Wise Distribution Reporting
- Improved Contracts Management with Real-Time Data
- Enhanced Transparency Across Distribution Processes
Benefits
- Streamlined Accounting with Project-Wise Insights
- Efficient Distribution Processes Across All Levels
- Accurate Tracking of Multi-Level Invoicing
- Improved Compliance with Government Regulations
- Real-Time Reporting for Better Decision-Making
- Enhanced Transparency in Contracts Management
- Optimized Operations with Centralized Data Management
Non Profit and Consulting Group
We successfully implemented ERPNext software for a Bangalore-based consulting and non-profit organization specializing in livelihood, health, and well-being initiatives. Acting as a Project Management Consultant, the organization required a robust system to streamline their operations. Our ERPNext solution enabled them to efficiently manage project planning, budgeting, and reporting, while also enhancing transparency and accountability across their initiatives. The implementation provided them with real-time insights, improved resource management, and better coordination, empowering them to deliver impactful results in their mission-driven projects.
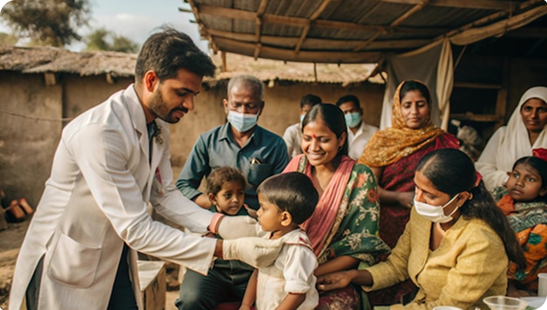
Challenges
- Fragmented Software Landscape with Quickbooks, Keka, Fyle
- Lack of Visibility into Project Progress and Profitability
- Duplication of Efforts in Management Reporting
- Manual Project Budgeting and SOE Preparation
- Difficulty Accessing Consolidated Data and Reports
- Inefficient Use of Multiple Software for Project Management
- Time-Consuming Reporting and Decision-Making Processes
Work Done
- Successful Go-Live with Project-Wise Budgeting in ERPNext
- Improved Budget Adherence and Progress Tracking
- Development of Expense Claims and Advance Request Applications
- Streamlined HR and Payroll Management
- CRM Integration for Walmart Vruddhi Project
- Comprehensive MIS Reporting for Better Insights
- Interactive Dashboards for Real-Time Monitoring
- Enhanced Financial Management Across Projects
Benefits
- Accurate Budgeting and Financial Tracking Across Projects
- Improved Adherence to Project Budgets and Timelines
- Efficient Expense Claims and Advance Management
- Streamlined HR Processes and Payroll Operations
- Enhanced Project Management with CRM Integration
- Data-Driven Decisions with MIS Reporting
- Real-Time Insights via Interactive Dashboards
- Optimized Financial Management and Resource Allocation
Luxury Accessories & Furniture Chain
We successfully implemented ERPNext software for a luxury accessories and furniture retail chain with stores in Delhi, Mumbai, and Bangalore, along with a strong digital presence across India. The ERPNext solution streamlined their operations, including inventory management, sales processes, and customer relationship management across multiple locations. By integrating their retail and digital channels, the company achieved real-time visibility into stock levels, seamless order processing, and enhanced customer experiences. This implementation has empowered them to operate more efficiently, reduce manual errors, and provide consistent, high-quality service to their clientele.
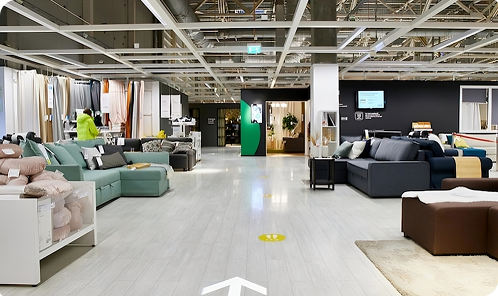
Challenges
- Heavy Reliance on Tally and Excel for Operations
- Challenges in Migrating Data for New Retail Stores
- Difficulty Connecting Purchasing, Quality, and Sales Data
- Lack of Direct Control Over Inventory Operations
- Time-Consuming Manual Reconciliation for Delivery Mistakes
- Absence of Consolidated Data Access and Reports
- Operational Bottlenecks Due to Disjointed Systems
- Limited Visibility Across Customer and Supplier Information
Work Done
- End-to-End Sourcing Process for Home Décor Items
- Simplified Retail Operations with Integrated POS
- Efficient Inventory Tracking and Product Variation Management
- Enhanced Financial Management with Reporting and Supplier Payments
- Automated Order Management and Invoicing Processes
- Streamlined Inventory Reconciliation for Reduced Errors
- Improved Operational Efficiency and Reduced Manual Work
- Better Decision-Making Through Financial and Inventory Insights
Benefits
- Efficient Sourcing and Supplier Management
- Seamless Retail Store Operations with POS Integration
- Accurate Inventory Tracking and Product Control
- Enhanced Financial Control and Decision-Making
- Time-Saving Through Automation of Key Processes
- Reduced Errors in Order and Inventory Management
- Improved Productivity with Streamlined Operations
- Real-Time Insights for Smarter Business Strategies
910, 72 Corp, Sakivihar road, Sakinaka Junction, Andheri East, Mumbai 72
Office AN 10, 1st Floor, Prozone Trade Center (PTC), Near Prozone Mall, Aurangabad Maharashtra 431006
506, Gera’s Imperium rise, Balaji Realty, 1029, Hinjawadi Phase 2 Rd, Hinjawadi Phase II, Hinjawadi Rajiv Gandhi Infotech Park, Hinjawadi, Pune, Pimpri-Chinchwad, Maharashtra 411057